Fleet Risk Management: A Comprehensive Guide

According to the National Safety Council (NSC), in 2022, medically consulted injuries from motor-vehicle incidents totaled 5.2 million, with total motor-vehicle injury costs estimated at $481.2 billion.
Running a fleet comes with a lot of moving parts—drivers, vehicles, routes, deadlines—and a whole lot of risk. One wrong move, whether it’s a crash, a missed inspection, or a tired driver pushing through a shift, can lead to real damage.
This blog is for fleet managers and operators looking to cut those risks. We'll walk through what fleet risk management is, where problems show up, and how to fix them.
What is fleet risk management?
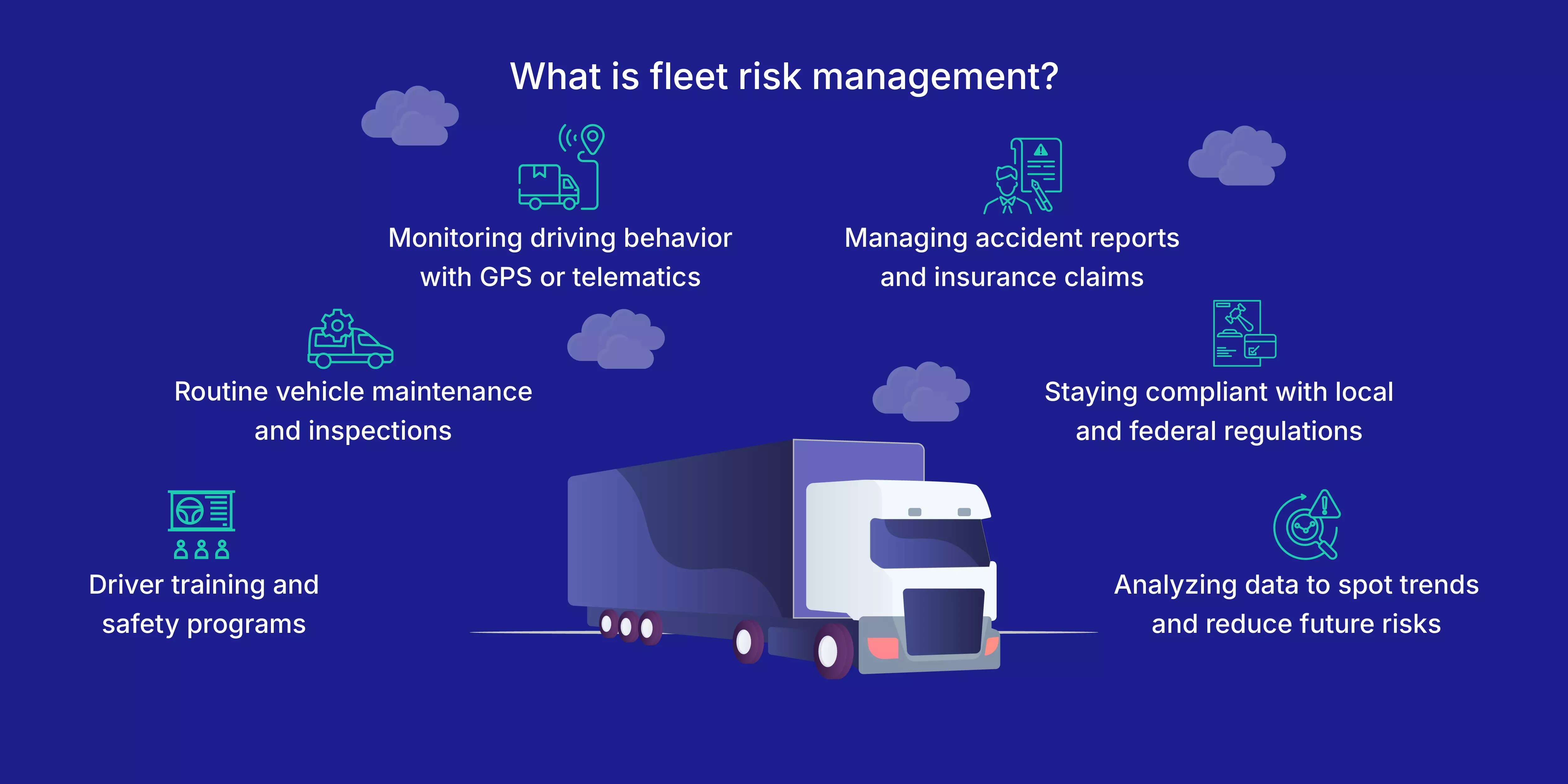
Running a fleet comes with a lot of moving parts, and things can go wrong fast. Fleet risk management is really just about spotting those trouble areas early—stuff like worn-out vehicles, risky driving, or missed inspections—and staying on top of them so they don’t snowball.
This can be as simple as checking that vehicles are in good shape, helping drivers follow the rules, and using tools to see how everything’s going day to day. It also includes handling any incidents that happen and making sure the company follows all the legal stuff.
Core parts of fleet risk management include:
- Driver training and safety programs
- Routine vehicle maintenance and inspections
- Monitoring driving behavior with GPS or telematics
- Managing accident reports and insurance claims
- Staying compliant with local and federal regulations
- Analyzing data to spot trends and reduce future risks
Types of risk in fleet management
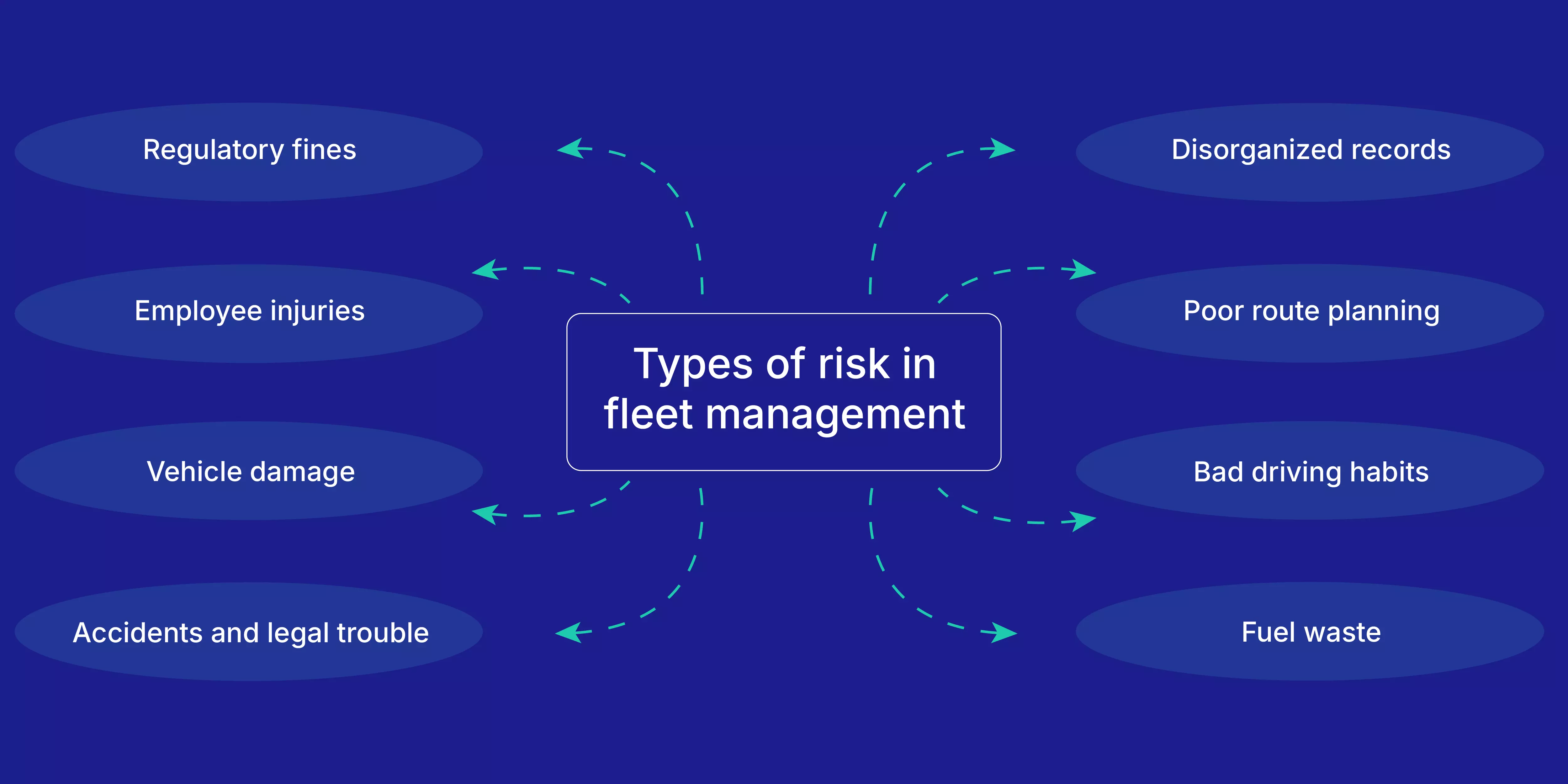
Here are the types of risk in fleet management:
1. Regulatory fines
Fleet operations are tied to strict rules—driver hours, vehicle inspections, licensing, and documentation. These rules aren’t static, and missing just one update can lead to costly penalties or downtime.
When no one’s assigned to track changes or follow up on paperwork, things fall through the cracks. It’s not just about avoiding fines—it’s about avoiding last-minute scrambles and operational delays that come with non-compliance.
2. Employee injuries
Drivers deal with long hours, poor weather, heavy loads, and unpredictable traffic—all of which raise the risk of getting hurt on the job. Injuries don’t just take a toll on people—they bring legal issues, lost workdays, and insurance claims.
Even experienced drivers can make split-second mistakes when fatigued or under pressure. Regular training, proper scheduling, and hazard awareness can reduce the chance of accidents that turn into HR and legal headaches.
{{demo_wms="/styles/components"}}
3. Vehicle damage
Even small mechanical issues—worn brakes, low fluids, underinflated tires—can turn into major failures if ignored. Add rough roads, overloaded cargo, or tight delivery deadlines, and the chances of vehicle damage shoot up.
Unplanned repairs mean missed routes and higher costs. Staying ahead with regular maintenance, quick repairs, and vehicle checklists can prevent breakdowns and keep the fleet where it belongs—on the road.
4. Accidents and legal trouble
A single crash can set off a chain of problems: insurance claims, vehicle loss, potential lawsuits, and even brand damage. If your driver is at fault, the fallout gets worse—and fast.
Insurance helps, but it won’t cover lost time or the hit to your reputation. Avoiding these risks means building solid safety policies, reviewing driving habits, and making sure every driver knows what’s expected.
5. Fuel waste
Fuel is one of the biggest operating costs—and it gets wasted in all kinds of ways. Long idling, poor route planning, aggressive driving, or filling up at the wrong place all add up over time.
Fuel theft also happens more often than people think. Tracking fuel usage closely, using fuel cards, and comparing vehicle performance week-to-week can highlight where the problem is before it drains your budget.
6. Bad driving habits
Unsafe driving doesn’t always show up right away. A few speeding events, sharp turns, or harsh brakes here and there might seem minor—but they wear down the vehicle and increase the chance of accidents.
Most drivers don’t notice they’re doing it unless someone shows them. That’s where driver behavior tracking and regular coaching come in. It's not about calling people out—it's about making the whole fleet safer.
7. Poor route planning
A poorly planned route means more than just a late delivery. It burns extra fuel, causes driver stress, and puts vehicles in riskier traffic conditions. Over time, it leads to wear and tear that could’ve been avoided.
Smart routing isn’t just for long hauls. Even local delivery fleets benefit from tools that help avoid traffic, reduce distance, and stay on schedule—without pushing drivers to rush.
8. Disorganized records
When you don’t know when a vehicle was last serviced—or whether a safety check was actually done—you’re flying blind. Missing logs or confused reports create issues during audits, breakdowns, or compliance checks.
Digital records fix that. You can quickly pull up inspection history, repair notes, or driver logs when needed. It’s one of those things that doesn’t seem urgent—until you really need it and it’s not there.
Importance of fleet risk management
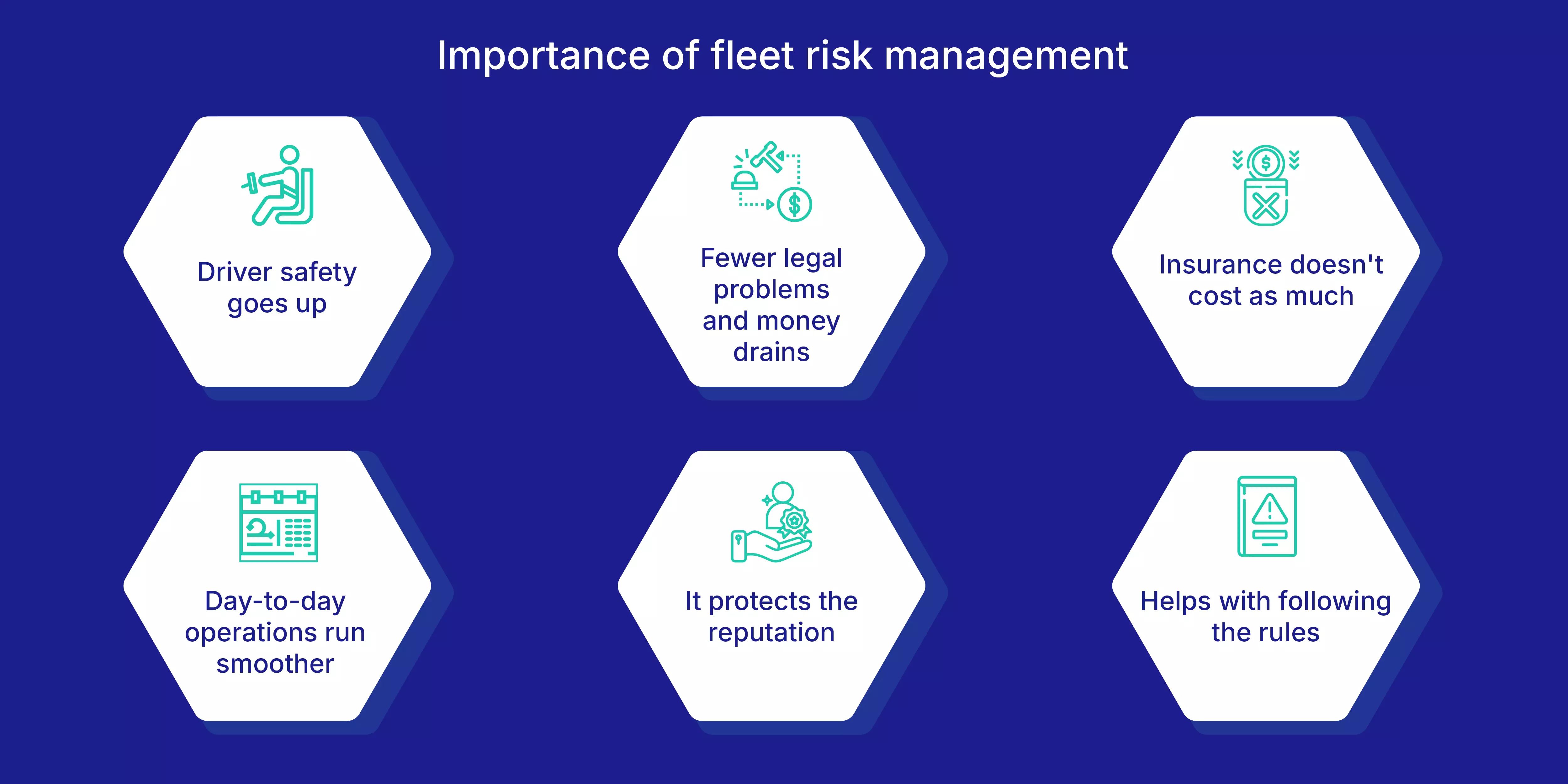
Implementing a strong fleet risk management program offers several key benefits for businesses:
1. Driver safety goes up
If drivers don’t feel supported or trained properly, mistakes happen. The idea here is pretty simple—keep them safe by checking in often, tracking how they drive, and offering training that actually sticks.
If someone’s always slamming the brakes or taking corners too fast, it shouldn’t take an accident to find out. Spotting that early can save a life. Over time, drivers learn to watch their habits, too. That’s where real change starts.
2. Fewer legal problems and money drains
Accidents can turn into lawsuits fast. And once lawyers get involved, costs start piling up. But if the company has good records—vehicle logs, driver training history, dash cam footage—it can show it did its part.
Say there’s a crash, but the footage proves your driver wasn’t at fault. That’s the kind of thing that keeps a company from getting pulled into a court battle or a huge payout. It’s not about avoiding blame—it’s about being ready to prove the truth.
3. Insurance doesn't cost as much
Insurance companies don’t like surprises. If you’ve got fewer claims, a clean safety record, and systems that track how the fleet is being run, that gives them confidence. They’ll usually lower the premium.
Some will even offer discounts if you're using dash cams or tracking tools. It's not a one-time thing—savings show up year after year, especially if the records stay clean.
4. Day-to-day operations run smoother
When a truck breaks down, it throws off everything. Deliveries are missed, calls start coming in, and drivers end up stuck or late.
A good risk plan helps avoid that mess. Regular checks, working sensors, and driver feedback all help keep vehicles on the road and out of the shop. Less downtime means fewer delays, fewer angry customers, and more jobs finished on time.
5. It protects the reputation
One bad crash or news story can stick around for a long time. If a fleet is always in the headlines for the wrong reasons—reckless driving, unsafe vehicles, late deliveries—clients start to worry.
Think of two service companies: one is known for showing up on time with clean vehicles and steady drivers. The other has three wrecks in a month. The choice is easy. People talk, and bad news travels fast. Fleet risk management helps keep that kind of attention off your back.
6. Helps with following the rules
Fleet operators deal with all kinds of regulations—driver hours, maintenance logs, and emissions checks. Forgetting one thing can lead to a fine or worse. Good risk management helps track what’s due and what’s been done.
No scrambling last minute to pass inspections. It’s less about checking boxes and more about knowing the business is covered if anyone asks for proof.
How to implement fleet risk management?
1. Know the laws and stay on top of them
When a fleet gets hit with surprise fines or penalties, it’s rarely due to anything complicated—it’s usually a missed document, an expired inspection, or a rule that changed and no one noticed. The hard part is that those rules don’t stay still. They shift by state, by vehicle class, and even by the type of cargo.
Here’s how to stay in the clear:
- Assign someone to track local, state, and federal regulations
- Use fleet software that flags deadlines and renewals
- Keep everything—licenses, inspections, audits—in one accessible place
- Set a calendar reminder for quarterly internal compliance checks
Regulations are like potholes—you don’t always see them coming, but they wreck everything if you hit one at speed.
2. Train drivers like it actually matter.
Let’s say a driver rear-ends someone because they were checking the GPS. Who’s at fault? The driver, sure—but also the person who didn’t prepare them for real-world distractions. Training is more than checklists and safety posters. It’s about helping people react to pressure without losing control.
Don’t overthink it. Try this:
- Host monthly “incident breakdowns” using real examples from your fleet
- Use the DEFENSE model: Distraction, Environment, Fatigue, Equipment, Navigation, Speed, Emergencies
- Pair drivers up for peer reviews (they’ll spot things management won’t)
Example: A delivery driver hit a parked car during a tight U-turn. During review, it turned out he’d been driving 9 hours straight. That falls under “Fatigue” in the DEFENSE model. Easy to overlook. Costly to ignore.
Training works when it feels relevant. Skip the classroom vibe. Talk like someone who’s been behind the wheel.
3. Monitor behavior with the right tools
Here’s the truth: if you don’t track it, you’ll only hear about it after something breaks. That’s too late. Telematics isn’t about catching drivers—it’s about understanding your fleet’s habits. You can’t solve blind spots if you don’t know where they are.
Quick ways to get started:
- Set up alerts for risky behavior (speeding, sudden stops, long idle time)
- Run weekly driving reports, but focus on trends—not one-off events
- Use visuals—heat maps or charts—to make feedback easier for drivers to understand
A telematics system flagged one truck idling 3x longer than the rest. Turns out the driver left it running while offloading because he didn’t know it made a difference. That’s the kind of small behavior that drains fuel—and budgets.
Not everything needs punishment. Some of it just needs a heads-up.
4. Stick to a real maintenance routine
This one’s not complicated. Every vehicle is being maintained or waiting to break. Missed oil changes, underinflated tires, unchecked brakes—they don’t just cause breakdowns. They cause accidents.
Keep it basic:
- Use a PMI (Preventive Maintenance Inspection) schedule
- Have drivers log pre- and post-trip checks (real ones—not just box-ticking)
- Store service history where everyone can find it—no binders in gloveboxes
Here’s how PMI looks in action:
Truck #18 gets checked every 5,000 miles—fluid levels, brakes, and tire wear. At 45,000 miles, the tech spots early disc wear. Repair gets logged and fixed the same week. No breakdown. No downtime. That’s how the system pays off.
If the wheels stop turning, everything else stops, too.
5. Watch fuel, as your budget depends on it
Fuel costs don’t explode overnight. They creep. One driver idles for 20 minutes. Another takes the long route. One bad fill-up at a premium station. No one notices… until your monthly fuel bill looks like a mistake.
Fuel waste isn’t always a fraud. Sometimes it’s just habits.
Tighten it up by:
- Issuing fuel cards with daily and per-transaction caps
- Tracking MPG per vehicle and flagging outliers
- Comparing fuel stops with actual GPS routes
Let’s say two identical trucks have a 3 MPG difference. That’s not nothing. Over 10,000 miles, that’s over 100 gallons wasted. Multiply that across 20 vehicles, and... well, you get the idea.
Margins are tight. Don’t let fuel eat into them quietly.
6. Have a plan for when things break down.
You don’t plan for emergencies while you’re in one. That needs to be done in advance. One driver stuck on the side of the road with no support is a risk. Ten of those? That’s a crisis.
Every fleet should have what’s basically an “oh sh*t” plan.
Cover the essentials:
- First call protocol—who the driver calls and who picks up
- Tow service and garage contacts on speed dial
- Step-by-step breakdown checklist (no assumptions)
- Template for incident reports—the driver shouldn’t have to wing it
Use the 3Cs model: Clear roles, Clean steps, and Consistent follow-up.
Example: A vehicle overheats on Route 78. The driver calls the dispatcher, who immediately calls the assigned garage. The tow arrives in 40 minutes. No delays, no chaos, and the next shift already has a backup vehicle. That’s how a system should run.
Tools for effective fleet risk management
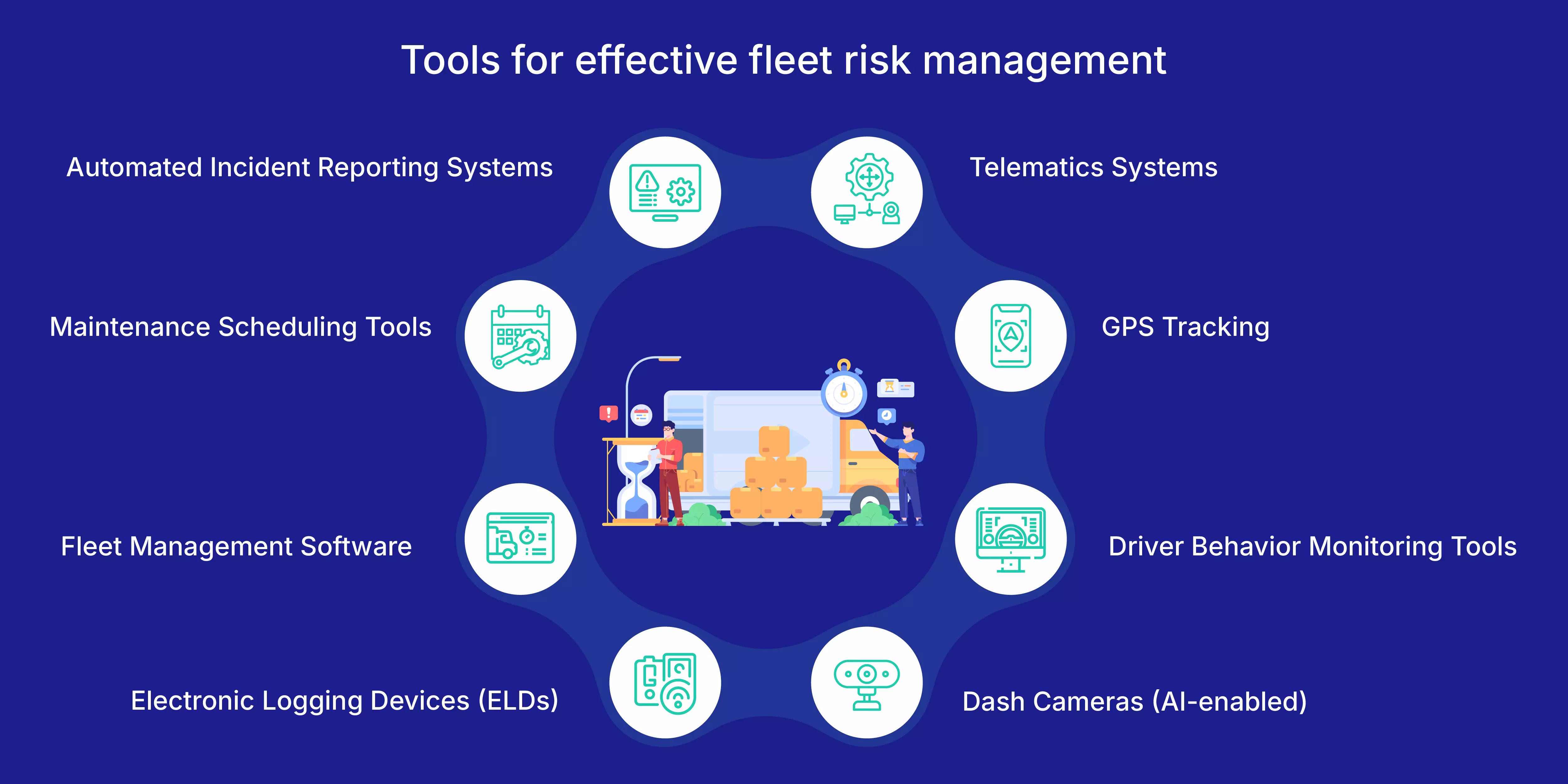
Here are some effectives tools to do risk management:
1. Telematics Systems
If you want to know what’s really happening out there—not just guess—telematics is the first tool you bring in. It pulls in data like vehicle speed, fuel use, braking, and more, all in real-time.
What you can do with it:
- Spot inefficiencies like excessive idling or speeding
- Get alerts when something’s off—like engine trouble
- Build a data trail for accountability
Example? One fleet noticed a driver was idling for nearly 40 minutes every morning during warm-ups. A simple chat saved gallons of fuel each week. That’s how fast the return can hit.
2. GPS Tracking
This one’s all about visibility. Knowing where your vehicles are at any given moment helps with everything from dispatching to safety.
You’ll use GPS to:
- Track location during deliveries
- Confirm ETA accuracy for customers
- Respond faster if a vehicle breaks down or goes off-route
It also saves the “where’s my order?” calls. Your ops team can just pull up the map.
3. Driver Behavior Monitoring Tools
You don’t need to babysit your drivers—but you do need to know how they’re driving. These tools track habits that raise red flags: harsh braking, sharp turns, speeding, and phone use.
What to watch for:
- Trends in aggressive driving
- Consistent issues with one vehicle or shift
- Risks that could raise insurance premiums
When used right, it’s not surveillance—it’s support.
4. Dash Cameras (AI-enabled)
This one’s a game-changer. You get actual footage of what happens before, during, and after an incident—but with AI doing some of the heavy lifting. It can detect distracted driving, yawning, phone use, and even smoking.
Use AI dash cams to:
- Catch risk behavior before it becomes a problem
- Protect your company if a driver is wrongly blamed
- Coach drivers using real moments from the road
Example: An AI cam flagged a driver looking down for 6+ seconds before drifting over the line. That footage helped the trainer show exactly what “distracted” looks like. Way more effective than any slideshow.
5. Electronic Logging Devices (ELDs)
These are now required for most commercial fleets in the U.S., and for good reason. They track how long a driver’s been on duty, ensuring compliance with Hours of Service rules.
How it helps:
- Keeps you compliant
- Cuts down on logbook errors
- Flags fatigue risks before they cause crashes
There’s no room for guesswork when it comes to driver hours. ELDs make it automatic—and audit-proof.
6. Fleet Management Software
Think of this as your fleet’s control room. All the data from your tools gets pulled into one dashboard where you can actually do something with it.
With a good platform, you can:
- Track vehicles, drivers, and routes in one place
- Set reminders for maintenance, renewals, or safety checks
- See reports that help you make better calls (not just guesses)
It’s where insight turns into action. No more juggling five apps and ten spreadsheets.
A platform like Fynd TMS brings a solid structure to daily fleet ops. You can onboard drivers, assign and track every order in real-time, and manage last-mile delivery with smart route configurations like single or multi-drop flows.
It also handles proof of delivery, scheduled drops, and even internal stock transfers between locations. So whether you're running groceries, furniture, or pharmacy shipments, your team gets full visibility—without switching between five different tools.
When all of that runs from one dashboard, decisions get faster, and chaos gets quieter.
7. Maintenance Scheduling Tools
Breakdowns are expensive. Scheduling tools help you stay ahead of them by setting up recurring checks, tracking service history, and assigning tasks.
Set these up to:
- Send alerts when a vehicle hits a mileage/service threshold
- Keep digital records of past maintenance
- Make sure nothing gets missed—no more “I thought someone else handled it.”
The payoff: fewer breakdowns, fewer surprise repairs, and a longer vehicle lifespan.
8. Automated Incident Reporting Systems
When something goes wrong on the road, the last thing you want is a sloppy paper trail. These tools let drivers log what happened fast—on the spot.
They help you:
- Record time, location, and details while it’s fresh
- Attach photos, dash cam clips, or sensor data
- Speed up internal reviews and insurance claims
And when it’s all digital, you don’t spend hours chasing down handwritten forms or calling five people for one story.
KPIs of fleet risk management
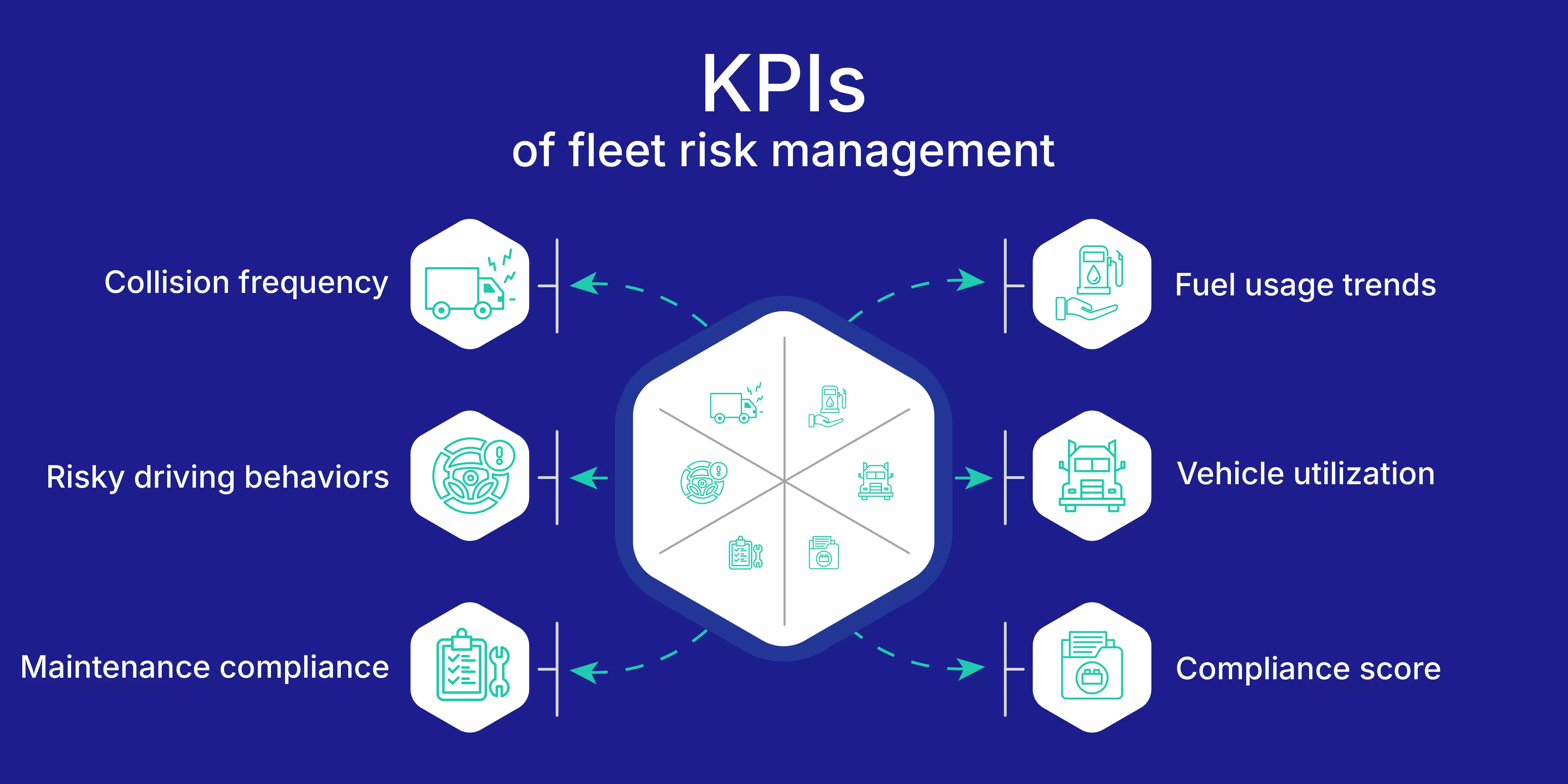
If you’re trying to figure out whether your fleet safety program is actually working, you’ve got to track the right stuff. Not every number matters—but a few do. These are the ones worth watching.
1. Collision frequency
Start with the basics: how often are your vehicles involved in crashes? This number tells you whether your drivers are actually staying safe or just getting lucky. You don’t just want the total number—track who’s involved, how often, and under what conditions. If one route or shift keeps showing up in reports, there’s your red flag.
2. Risky driving behaviors
Speeding. Hard braking. Rapid acceleration. These aren’t just annoying—they’re signs of risky habits that lead to wrecks. Use telematics or driver behavior tools to log this stuff. You’re not looking to punish drivers. You’re looking for patterns so you can coach smarter.
Example: If Driver A racks up 15 speeding events in one week but no one says anything, you’re gambling with every shift they drive.
3. Maintenance compliance
A truck that skips maintenance isn’t just running rough—it’s one busted brake line away from disaster. Track how often scheduled checks are happening on time. Missed inspections or late oil changes? That’s a management issue, not just a technician problem.
Set up alerts and monitor completion rates for regular servicing. A 100% compliance rate might be unrealistic, but 60% is a problem.
4. Fuel usage trends
If fuel costs are climbing but delivery volume stays the same, something’s off. It could be idling, bad routing, or worse—unauthorized stops. Compare fuel spend per vehicle or route. If one truck burns way more gas than the others, dig in.
Fuel KPIs aren’t just about budget—they show how tight your operations are running.
5. Vehicle utilization
Are all your trucks being used efficiently? Some fleets keep too many backups on hand, which means insurance, storage, and depreciation costs for vehicles that barely move. Track usage by miles driven or hours on the road. If something’s consistently underused, rethink whether you need it—or if routes need rebalancing.
6. Compliance score
Whether it’s driver logs, inspection records, or safety policies, being able to show you’re following the rules is huge. Create a score based on how well your team is meeting legal requirements. This could include ELD compliance, hours of service, and DVIR submissions.
Challenges of fleet risk management and their solutions
Managing a fleet isn't just about keeping vehicles on the road; it's about navigating a maze of risks that can derail operations. Here's a look at some common challenges and practical ways to tackle them.
1. Inexperienced or poorly trained drivers
You can have the best vehicles and tracking systems in the world, but if the driver doesn’t know how to handle pressure—or even basic road risks—it all falls apart. New hires without proper training are a real risk, especially under time pressure.
What to do:
- Run scenario-based training: night routes, bad weather, sharp turns in tight streets
- Do live refreshers, not just online modules
- Pair rookies with experienced drivers for shadow runs the first week
If you’re not putting in the time upfront, you’ll pay for it later—in repairs, downtime, or worse.
2. No clear view of where assets are
Not knowing where your trucks are is more common than it should be. Dispatchers get flooded with calls. Drivers go off-route. Deliveries are late. Stuff gets missed.
The fix:
- Use GPS that shows real-time location
- Set up geofencing alerts for when vehicles enter or leave zones
- Track driver status live—en route, stopped, off-duty
This isn’t about control. It’s about staying ahead of problems before the customer calls asking where their order is.
3. Driver fatigue (and no one realizes until it’s too late)
Drivers push past their limits. Sometimes, because they want to finish the shift. Sometimes, because they feel like they have to, but that decision is where accidents start.
How to cut this off early:
- Enforce breaks—don’t just suggest them
- Use ELDs (Electronic Logging Devices) to track rest periods automatically
- Watch for signs in driver behavior—slower reaction times, inconsistent routes
One driver nodded off at a stoplight after a 12-hour run. No crash, luckily—but it was the last shift he drove without a solid break policy in place.
4. Weak maintenance follow-up
One missed oil change turns into a blown engine. One ignored brake check leads to a near miss. If your team’s relying on memory or sticky notes to manage vehicle health, something’s going to get missed.
How to clean it up:
- Use a digital log that tracks the maintenance history
- Set mileage- or hour-based service reminders
- Make pre-trip checks mandatory (and audit them occasionally)
Downtime doesn’t just cost money. It puts pressure on the rest of the fleet to cover, and that creates more risk.
5. Too many rules, not enough clarity
Regulations are everywhere—driver hours, emissions, inspections. One missed form or expired certification, and you’re looking at a fine or worse. But the bigger issue? Most teams aren’t 100% clear on what’s required—or who’s in charge of tracking it.
Here’s how to stay ahead:
- Assign one person to own compliance (not “everyone”)
- Run internal audits quarterly
- Use a tool or shared calendar to track all deadlines
Don’t assume it’s handled. Make sure it is.
6. Data but no security plan
The more tech you plug into your fleet, the more data you’re collecting. And if that data isn’t protected, you’ve got a new kind of risk—cyber.
How to stay covered:
- Use software with solid encryption and access controls
- Train your staff on phishing and login safety
- Keep devices and systems updated—don’t delay patches
It’s not just about protecting your fleet—it’s about protecting your customers and your company’s name.
Fleet risk management vs compliance
Fleet risk management is the bigger picture. It’s everything a company does to keep vehicles, drivers, and operations safe—from training and tech to tracking behavior and planning for breakdowns.
Compliance, on the other hand, is about following the rules set by federal and state agencies. In the U.S., this mostly means sticking to FMCSA regulations: Hours of Service (HOS), DOT inspections, ELD mandates, driver qualification files, and vehicle maintenance logs.
Think of it this way:
- Compliance helps you avoid fines and stay legal
- Risk management helps you avoid accidents, downtime, and lawsuits
One is required. The other is smart. The best fleets do both.
Managing a fleet comes with risks, but it doesn’t have to feel out of control. With the right tools and a clear plan, you can prevent a lot of problems before they happen—and handle the rest without scrambling.
If you're ready to make day-to-day delivery management easier, Fynd TMS gives you what you need to keep things moving: live tracking, better routes, and fewer surprises.
Frequently asked questions
It depends on your setup, but many fleets spend several thousand dollars per vehicle each year.
You add up everything—fuel, maintenance, insurance, wages—and see what it’s costing you to run.
It’s a way to figure out what a vehicle really costs from purchase to resale, including all the stuff in between.
Stay ahead on maintenance, avoid fuel waste, plan better routes, and keep an eye on how vehicles are used.